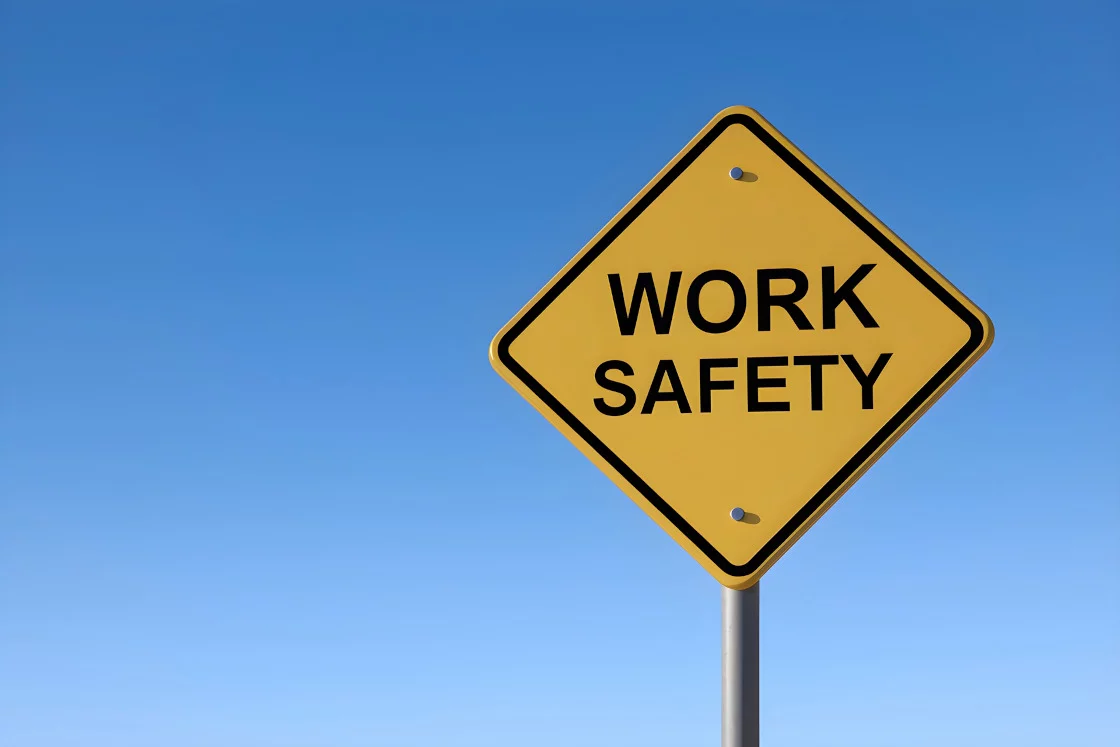
Workplace safety is often viewed as a compliance checkbox—a necessary step to meet legal requirements. But beneath the surface, neglecting health and safety standards has a more sinister consequence. Small, overlooked risks like dust exposure, excessive noise, or cluttered workspaces slowly accumulate, causing long-term damage to your workers’ health, your company’s reputation, and your bottom line. These “silent killers” don’t just harm individuals—they erode businesses from within.
The Hidden Dangers Lurking on Your Worksite
Worksites often present obvious hazards like heavy machinery and elevated work areas, but the most dangerous risks are often hidden in plain sight. Dust particles, excessive noise, and poor housekeeping may seem insignificant on a daily basis but accumulate over time to create serious health and safety challenges. These silent threats not only jeopardize workers’ well-being but also expose businesses to costly fines, legal liabilities, and productivity losses. Addressing these dangers requires proactive measures and consistent oversight to ensure a safe and efficient work environment.
How Do Dust Containment Systems Protect Your Worksite?
Dust containment systems, like industrial vacuum units and water suppression techniques, capture and minimize airborne particles that can harm workers. These systems are critical in industries where materials like silica, concrete, or wood dust are prevalent, as they prevent respiratory issues such as silicosis and asthma. Effective containment not only ensures worker safety but also keeps the worksite compliant with safety regulations by maintaining acceptable air quality levels.
Why Are Advanced Noise Barriers Essential?
Advanced noise barriers and sound-dampening panels significantly reduce the impact of high-decibel machinery on worksites. By absorbing or deflecting sound waves, these barriers protect workers from long-term hearing loss caused by prolonged exposure to noise above safe thresholds. Additionally, they ensure the noise levels stay within legal limits, reducing the likelihood of complaints or penalties while maintaining a more productive work environment.
What Role Does Tool and Equipment Maintenance Play in Safety?
Proper maintenance of tools and machinery prevents excessive noise and dust generation caused by wear and tear. For instance, dull blades or poorly maintained motors can produce higher noise levels or malfunction, increasing the risk of accidents. Regular inspections and servicing ensure that equipment operates efficiently, reducing safety hazards and minimizing downtime due to unexpected failures.
Why Are PPE Compliance Checks Non-Negotiable?
Personal protective equipment (PPE) like respirators and earplugs is only effective if it functions as intended. Regular inspections ensure that PPE meets safety standards and remains in good condition, free from defects or wear. Ensuring workers are using the correct PPE for specific tasks further reduces risks from exposure to dust, fumes, or noise, making compliance checks a crucial component of workplace safety.
How Do Designated Walkways Reduce Accidents?
Designated walkways provide clear, unobstructed paths for workers to navigate busy worksites safely. These pathways help reduce slips, trips, and falls by organizing traffic flow and keeping hazardous areas separate. They also ensure emergency exits remain accessible at all times, allowing for quick evacuations in critical situations. Regular inspection and maintenance of walkways further enhance their effectiveness in preventing accidents.
How Do Ventilation Systems Improve Air Quality on Worksites?
Ventilation systems promote a constant flow of clean air, reducing the concentration of harmful dust, fumes, and other airborne contaminants. These systems are particularly vital in enclosed spaces where poor airflow can lead to health risks like respiratory irritation or oxygen deficiency. Proper installation and regular maintenance ensure that the systems operate effectively, creating a safer and healthier work environment for employees.
How Do Waste Disposal Protocols Enhance Worksite Safety?
Daily waste disposal protocols prevent the accumulation of debris that can create slip and trip hazards. By systematically removing waste, worksites stay organized, reducing the likelihood of accidents and ensuring a cleaner, more efficient environment. Proper disposal also minimizes fire risks associated with flammable materials, protecting both workers and the property.
Why Is Emergency Spill Response Training Crucial?
Emergency spill response training equips workers to handle hazardous material leaks quickly and effectively. With proper training and access to spill kits, workers can contain spills before they spread, reducing the risk of injuries, environmental contamination, and potential regulatory violations. Prepared teams ensure that even unexpected spills are managed safely and efficiently.
What Makes Fall Protection Systems Non-Negotiable?
Fall protection systems, such as guardrails, harnesses, and scaffolding, are critical for safeguarding workers at heights. These systems prevent falls, which are one of the leading causes of workplace injuries and fatalities. Ensuring equipment is installed correctly and regularly inspected significantly reduces risks, creating a safer environment for employees working on elevated surfaces.
How Does Lighting Optimization Improve Worksite Safety?
Adequate lighting eliminates shadows and dim areas, improving visibility across the worksite. This reduces the risk of accidents such as trips, falls, or improper equipment usage in poorly lit spaces. Proper lighting also enhances accuracy during tasks, ensuring workers can perform their jobs safely and efficiently, particularly in high-risk environments.
Why Is Noise Level Monitoring Important?
Monitoring noise levels with decibel meters ensures that worksites remain within permissible exposure limits, protecting workers from noise-induced hearing loss. Regular monitoring allows management to identify areas where noise reduction measures, such as barriers or equipment maintenance, are needed. Proactively addressing noise levels prevents long-term health issues and ensures compliance with safety regulations.
How Do Scheduled Hazard Audits Mitigate Risks?
Regular hazard audits identify potential risks before they become serious issues. By systematically reviewing equipment, procedures, and environmental factors, audits provide actionable insights that allow management to address hazards proactively. Scheduled audits ensure that safety standards are consistently maintained and that emerging risks are promptly mitigated.
What Role Does Housekeeping Accountability Play in Safety?
Assigning dedicated teams to oversee housekeeping ensures that worksites remain clean, organized, and hazard-free. This accountability reduces risks associated with clutter, such as trips, falls, and blocked emergency exits. Consistent oversight fosters a culture of safety and efficiency, ensuring that every worker understands the importance of maintaining a tidy and safe work environment.
How Do Ergonomic Workstations Improve Worker Safety?
Ergonomic workstations, designed with adjustability and worker comfort in mind, reduce the risk of musculoskeletal injuries caused by repetitive tasks or improper posture. These setups support proper body alignment, minimize strain, and enhance productivity by allowing workers to perform their duties efficiently and without discomfort. Implementing ergonomic solutions also decreases absenteeism due to work-related injuries, fostering a healthier workforce.
Why Are Fire Risk Assessments Essential on Worksites?
Fire risk assessments identify flammable materials, evaluate storage practices, and pinpoint fire hazards on worksites. This proactive approach minimizes the risk of fire outbreaks by ensuring that combustible items are stored safely and that ignition sources are controlled. Regular fire drills and the availability of fire extinguishers further enhance readiness, ensuring workers can respond quickly and effectively to emergencies, reducing potential damage and injury.
Why Ignoring These Risks is Costlier Than You Think
Overlooking health and safety risks on your worksite may save time and effort in the short term, but the long-term consequences can be devastating. The costs aren’t limited to immediate medical bills—they ripple across every aspect of your operations, impacting productivity, finances, and reputation. When workers are injured or become ill due to workplace hazards, their ability to perform at full capacity is compromised. This slows down operations, causes delays, and increases the workload for others, creating inefficiencies across the board. In severe cases, absenteeism due to health issues can leave critical tasks unfulfilled, jeopardizing deadlines and profitability.
Failing to meet occupational health and safety standards exposes businesses to significant legal risks. Regulatory fines, lawsuits from injured employees, and compensation claims can quickly add up, draining resources and impacting cash flow. These legal battles are not only expensive but can also disrupt daily operations, further compounding the financial strain. A poor safety record doesn’t just hurt your workers—it hurts your brand. Clients and partners may reconsider doing business with a company known for neglecting safety standards, while talented workers may avoid joining your team. Reputation loss is hard to rebuild and can lead to decreased opportunities and lower market competitiveness.
Workplace hazards often result in chronic illnesses or long-term injuries, leading to ongoing insurance claims and higher premiums. These persistent costs can become a financial burden, especially for smaller businesses. Additionally, the indirect expenses of rehiring and retraining new employees to replace those affected add to the long-term impact. Ignoring workplace safety doesn’t just create risks—it creates lasting consequences that affect every facet of your business. Proactive investment in health and safety is not just a regulatory necessity; it’s a smart financial and operational decision that protects your workers and your bottom line.
How Health and Safety Expertise Can Help
A proactive approach to health and safety is essential for addressing both immediate hazards and long-term risks. Health and safety experts play a critical role in identifying, mitigating, and managing these dangers to create safer workplaces and ensure regulatory compliance.
many health and safety experts conduct comprehensive audits to uncover risks that often go unnoticed. These include issues like poor ventilation for dust control, uncalibrated noise levels, and inadequate housekeeping practices. Regular audits provide actionable insights that help businesses implement targeted safety measures while ensuring compliance with occupational health and safety regulations.
Experts design and implement solutions to prevent hazards before they escalate:
- Ventilation systems, respirators, and dust suppression methods, such as wet cutting, minimize airborne particles.
- Installing sound barriers, maintaining machinery, and providing hearing protection help reduce harmful noise exposure.
- Clear housekeeping policies ensure organized, hazard-free workspaces that reduce slips, trips, and falls.
Educating workers is key to maintaining long-term safety. Training programs equip employees with the knowledge to identify risks, use protective equipment effectively, and respond to emergencies. These initiatives build a culture of safety where employees take proactive roles in preventing accidents and hazards on-site.
Health and safety expertise transforms workplaces by addressing risks at their root, fostering a safer environment, and ensuring compliance with legal standards. Investing in professional guidance not only prevents incidents but also strengthens the overall productivity and resilience of your operations.
Taking Action: Steps to a Safer Worksite
- Start with an Audit: Identify hazards specific to your worksite through a professional health and safety assessment.
- Invest in Safety Measures: Allocate resources for preventative solutions like dust control systems and noise management.
- Enforce Cleanliness: Implement strict housekeeping protocols to eliminate accidents caused by clutter.
- Educate Your Team: Conduct regular training sessions to keep safety knowledge fresh and actionable.
- Monitor and Adjust: Continuously assess and adapt safety measures as new challenges arise.
The silent killers on your worksite may not make headlines today, but their long-term consequences can cripple your business and endanger your workers. By investing in health and safety expertise, you can protect your team, your reputation, and your future.
Don’t wait for a crisis to force your hand. Start addressing these risks today and create a safer, healthier workplace for everyone. Because when it comes to workplace safety, prevention is always better—and cheaper—than the cure.